Fatigue Testing for Biomedical Implants: Advances and Challenges
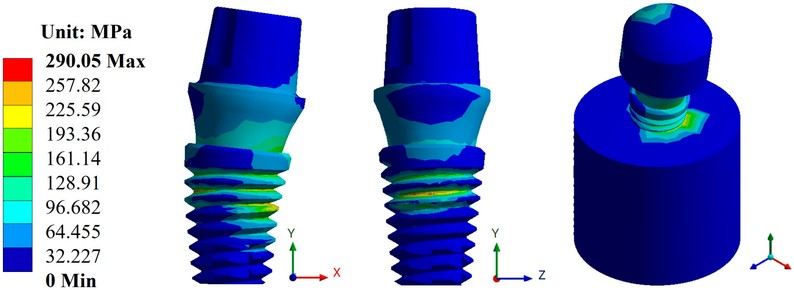
In the realm of biomedical engineering, ensuring the durability and reliability of implants is crucial. One key aspect of this evaluation is fatigue testing, a process that assesses how implants perform under repeated stress over time. This article delves into the advances and challenges in fatigue testing for biomedical implants, highlighting its importance in ensuring implant safety and longevity.
Understanding Fatigue Testing
Fatigue testing is designed to simulate the conditions an implant will face during its functional lifetime. Unlike static testing, which measures an implant’s strength at a single point in time, fatigue testing evaluates how the implant withstands cyclic loads. This is particularly important for implants subjected to dynamic forces, such as those used in orthopedic, dental, and cardiovascular applications.
The goal is to identify potential failure modes and predict the lifespan of the implant. By subjecting the implant to repeated loading and unloading cycles, researchers can assess its resistance to fatigue, which can lead to cracks, fractures, or even complete failure.
Advances in Fatigue Testing Technologies
- Enhanced Material Testing
Recent advancements in material science have led to the development of more durable and biocompatible materials for implants. Modern fatigue testing methods can now accommodate these advanced materials, providing a more accurate assessment of their performance. For instance, advanced polymers and composites are being tested to evaluate their resistance to fatigue and their long-term stability in the human body.
- Improved Testing Equipment
Technological innovations have greatly enhanced the precision and capabilities of fatigue testing equipment. State-of-the-art fatigue testing machines now offer higher accuracy in simulating real-life conditions. These machines can replicate complex loading scenarios, including multi-axial stress, which is crucial for understanding how implants perform under various types of stress.
- Computational Modeling and Simulation
Computational modeling has become an indispensable tool in fatigue testing. Finite Element Analysis (FEA) and other simulation techniques allow researchers to model the behavior of implants under cyclic loads without the need for extensive physical testing. This approach not only speeds up the testing process but also provides valuable insights into potential failure points and the overall performance of the implant.
- Real-Time Monitoring and Data Collection
Advancements in sensor technology have enabled real-time monitoring of implants during fatigue testing. Sensors embedded within the implants or testing apparatus can provide continuous data on stress, strain, and other critical parameters. This data helps researchers understand the implant’s behavior under load and identify any signs of wear or potential failure.
Challenges in Fatigue Testing for Biomedical Implants
- Complexity of Biological Environments
One of the primary challenges in fatigue testing is accurately simulating the complex biological environment in which implants operate. The human body presents a dynamic and variable environment, including factors such as body temperature, fluid interactions, and tissue integration. Replicating these conditions in a laboratory setting is challenging, and discrepancies between the testing environment and the actual biological environment can lead to inaccuracies in test results.
- Variability in Patient Anatomy
Implants are often designed to fit a wide range of anatomical structures. Variability in patient anatomy can affect the stress distribution and loading conditions experienced by the implant. Standardized testing procedures may not account for all anatomical variations, potentially leading to incomplete assessments of an implant’s performance across different patient populations.
- Long-Term Testing and Durability
Fatigue testing typically involves subjecting the implant to repeated cycles over a relatively short period. However, the true lifespan of an implant may extend over several years or even decades. Conducting long-term fatigue tests that accurately reflect the entire lifespan of an implant is both time-consuming and resource-intensive. This challenge is exacerbated by the need for testing to account for changes in material properties and mechanical behavior over time.
- Integration of New Technologies
As new materials and technologies are introduced into the field of biomedical implants, there is a constant need to update and adapt testing methods. Integrating new technologies into existing fatigue testing protocols can be complex and requires ongoing research and development to ensure that testing methods remain relevant and effective.
- Regulatory and Standardization Issues
Fatigue testing for biomedical implants is governed by various regulations and standards, which can vary by region and application. Ensuring compliance with these standards while also innovating and improving testing methods can be a challenging balancing act. Additionally, the lack of standardized testing procedures across different organizations can lead to inconsistencies in data and evaluation.
The Future of Fatigue Testing for Biomedical Implants
The future of fatigue testing for biomedical implants holds promise with ongoing advancements in technology and methodology. Key areas of development include:
- Personalized Testing Approaches
As personalized medicine becomes more prevalent, there is a growing interest in developing testing methods that account for individual patient differences. Personalized fatigue testing could provide more accurate predictions of implant performance based on specific patient anatomy and loading conditions.
- Integration of Artificial Intelligence
Artificial Intelligence (AI) and machine learning are poised to revolutionize fatigue testing. AI algorithms can analyze large datasets from fatigue tests to identify patterns and predict failure modes with greater accuracy. This integration could lead to more efficient and effective testing procedures.
- Advancements in Material Science
Continued research in material science will likely yield new materials with enhanced fatigue resistance and biocompatibility. These materials may require new testing methodologies to fully understand their performance and ensure their safety in clinical applications.
- Enhanced Simulation Techniques
As computational power increases, simulation techniques will become more sophisticated, allowing for more detailed and accurate modeling of implant behavior. This will enable researchers to predict implant performance more effectively and reduce the need for extensive physical testing.
Conclusion
Fatigue testing is a critical component in the development and evaluation of biomedical implants. While significant advances have been made in testing technologies and methodologies, challenges remain in accurately simulating biological environments, accommodating anatomical variability, and ensuring long-term durability. Ongoing research and technological advancements hold the promise of addressing these challenges and improving the reliability and safety of biomedical implants. By continuing to innovate and refine fatigue testing practices, the field of biomedical engineering can better ensure the success and longevity of implants in improving patient outcomes