The Role of AI and IoT in Predictive Maintenance vs. Preventative Maintenance
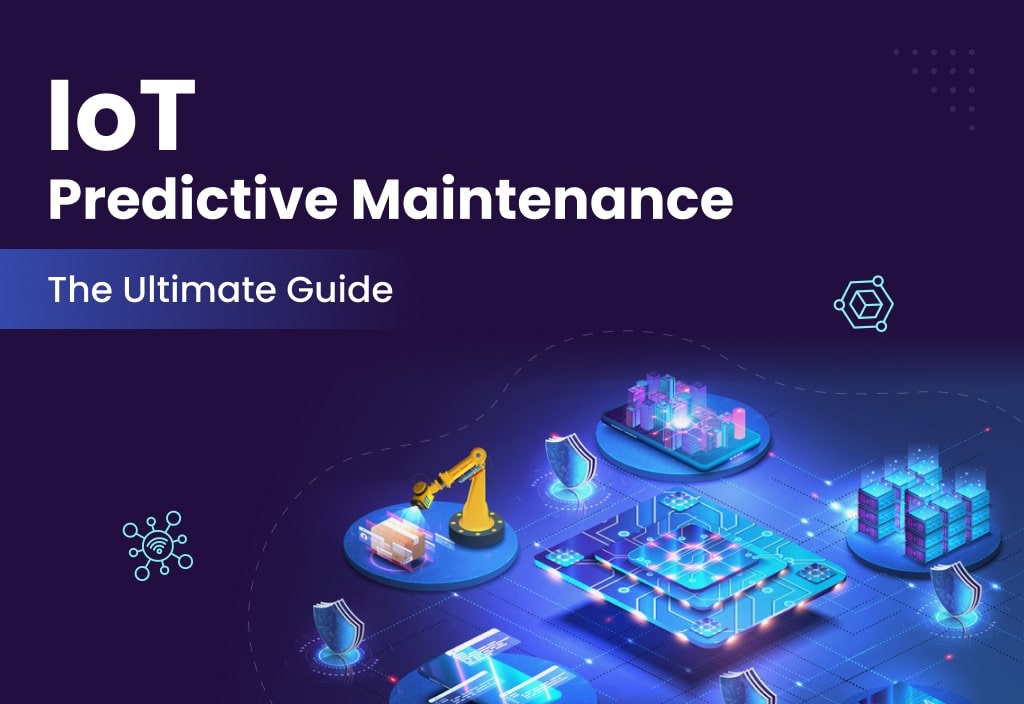
Preventative maintenance (PM) involves scheduled maintenance checks regardless of the equipment’s condition. Manufacturer recommendations, historical data, and industry best practices usually inform this schedule. PM tasks include lubrication, filter changes, inspections, and component replacements. Preventative maintenance extends equipment life and avoids breakdowns, but it also wastes money and disrupts operations.
Predictive Maintenance: An Approach Based on Data
Predictive maintenance (PdM) employs a more proactive strategy by forecasting when equipment failure is likely to happen through condition monitoring and data analysis. This minimizes downtime and maximizes resource allocation by enabling maintenance to be carried out only when required. The ability to gather and evaluate pertinent data from equipment in real-time is essential for efficient PdM. This is where the Internet of Things (IoT) and artificial intelligence (AI) work together.
The AIoT Revolution: A Change in Maintenance Perspective
Predictive maintenance is being revolutionized by AIoT, the term for the marriage of AI and IoT. IoT sensors are installed on machinery to gather a variety of data, such as sound, vibration, temperature, and pressure. After that, the data is sent to a central platform, where AI algorithms examine it to find trends, abnormalities, and possible causes of failure. AI is able to identify minute variations in equipment performance that humans might overlook. AI’s predictive powers can help you better understand the condition of your equipment before it’s too late.
Improving Predictive Accuracy with AI-Powered IoT Solutions
Predictive maintenance accuracy is greatly increased by AI-powered IoT solutions. AI algorithms can adjust to the unique operating conditions and performance history of each piece of equipment, unlike traditional techniques that depend on set timetables. When comparing iot predictive maintenance vs preventative maintenance, IoT-driven predictive methods stand out for their ability to forecast issues before they occur, reducing unnecessary interventions. AI can more accurately forecast errors and uncover intricate links by evaluating enormous volumes of data. This results in decreased downtime, better resource use, and more efficient maintenance interventions.
Exceeding the Standard Preventive Actions
AI-driven predictive maintenance outperforms traditional preventative efforts in several ways. It reduces unnecessary maintenance, lowering costs and operating disturbance. Second, it allows for more targeted maintenance, preventing breakdowns. Third, it prevents catastrophic failures and optimizes maintenance programs to extend equipment life. AI enhances machine learning, improving data set predictions.
Conclusion
Predictive maintenance is changing as a result of the convergence of AI and IoT, becoming a more precise, effective, and economical strategy. AI-driven IoT solutions are helping businesses adopt a proactive, data-driven maintenance approach by utilizing the power of data analysis and machine learning. This is in contrast to traditional preventative maintenance. The future of maintenance will be more concerned with anticipating and preventing equipment breakdowns, increasing uptime, and optimizing resource use as AI and IoT technologies develop further.